Reshoring and nearshoring manufacturing provide corporations with higher quality and security and better delivery timeframes.
Delivering precision-engineered manufacturing solutions with reliability and timeliness to our industry-leading customers is core to the promise of The Partner Companies’ specialty manufacturers. TPC continually evaluates our business practices and evolves our approach to deliver consistently excellent results.
One of our current efforts includes the process of reshoring or nearshoring many of the raw materials we utilize for our customers in the defense, renewable energy, medical, and technology industries.
“We’ve been looking at the factors that impact how our specialty manufacturers serve their customers,” reports TPC Supply Chain Director Sue Lech, “and how we can improve manufacturing efficiencies and pricing. The availability of materials and components from overseas suppliers is at the top of that list, so reshoring and nearshoring are strategic initiatives for us.”
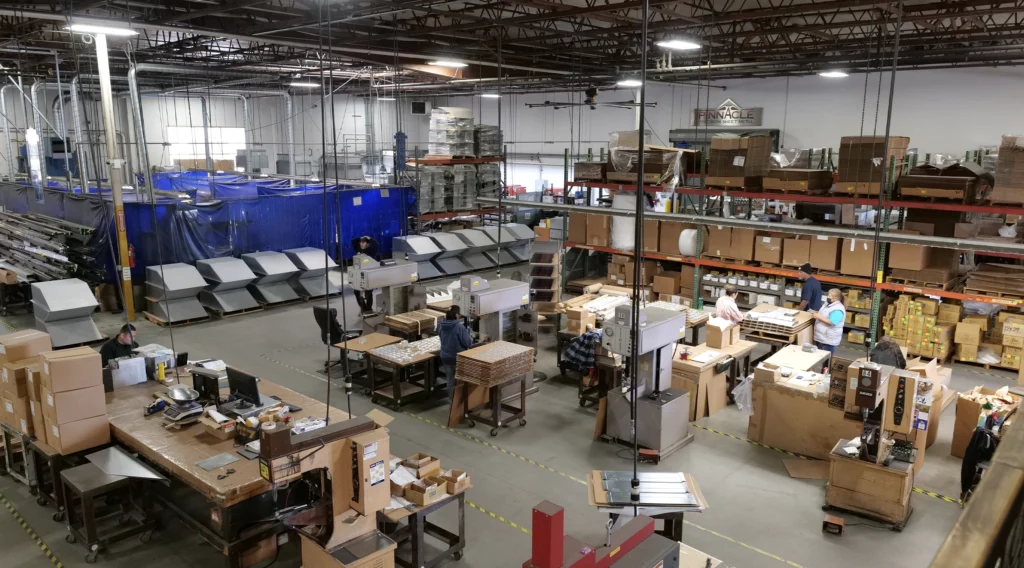
A Brief on Offshoring, Reshoring, and Nearshoring
The idea of looking for economic efficiencies is as old as mercantile exchanges, but offshoring manufacturing and raw material production began in earnest during the 1970s and 1980s.
During those decades, the production of consumer goods, electronics, automotive and industrial parts, and many other goods occurred overseas. Corporations benefited from lower labor and resource costs, improving profit margins and bottom lines. The boom of online communications during the 1990s increased efficiency and comfort for many corporations.
Likewise, raw materials were readily available overseas, heightening the demand for more and more overseas production.
Offshoring peaked in the early 2000s, but by the mid-2010s, the trend of reshoring — returning business and manufacturing operations to the United States — and nearshoring (moving operations to geographical neighbors) started.
“Geopolitical, shipping, time, and logistics issues were just some of the reasons companies began looking back to a U.S. manufacturing solution,” says Lech.
Acts of nature (the earthquake and tsunami in Japan in 2011 and the COVID-19 pandemic) and man (Russia’s invasion of Ukraine) also significantly impacted global supply chains, driving corporate and public efforts to return manufacturing to the United States.
The Benefits of Reshoring/Nearshoring
In our early days of reshoring and nearshoring, The Partner Companies’ specialty manufacturers see improved material quality control, lead times, and reduced shipping costs. As a whole, TPC believes that the more pieces of the manufacturing process it returns to the United States, the more positive an impact it will have on climate change and hiring numbers where its production centers are located.
Just as importantly, TPC can ensure higher material, part, component, and assembly security for our customers who produce mission-critical solutions for the defense industry because we have a higher level of traceability. (Read more about TPC and Traceability here.)
Regarding jobs, The Reshoring Initiative, an organization advocating for the return of manufacturing to the United States, reports that the number of reshoring job announcements in 2022 jumped 53%, the highest rate ever recorded.
What Companies Should Consider Before Reshoring/Nearshoring
Non-governmental organizations, chambers of commerce, and departments in the United States government are focused on proving that reshoring and nearshoring are essential to growing the U.S. economy.
To be fair, there are pluses and minuses. Because of additional costs in labor and materials, many products made in the United States will cost more to consumers. Some companies may find that a “value” promise is more important than a locally produced promise.
Harry Moser from The Reshoring Initiative encourages companies looking to return manufacturing to the United States to consider several factors when determining if it makes sense:
- Total landed cost, including packaging, duty, freight, freight fees, and insurance
- Inventory carrying cost
- Risk of product obsolescence
- Travel cost
- Quality assurance
- Opportunity costs (when materials aren’t available or products are delivered late)
- Environmental impact
- Intellectual property threats
Ready to Bring Your Manufacturing Home?
TPC senior management is leading the company’s efforts to reshore and nearshore and will share our experience and expertise as you look to bring manufacturing back to the United States.
Contact us to get started.